Glued iPhone batteries may be a thing of the past, if this new tech works out
Apple is reportedly testing ways to make it a lot easier for users to remove the glue holding down the battery in the iPhone, with a report suggesting the new tech may arrive as soon as the iPhone 16.
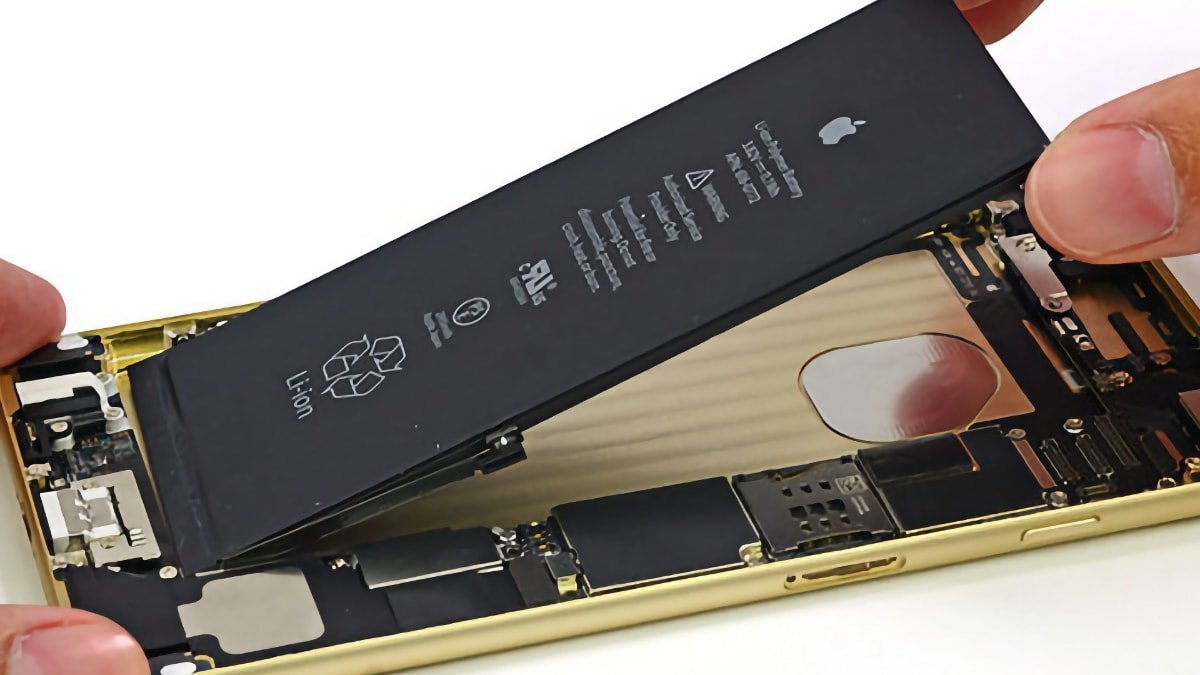
Pulling a battery out of an iPhone
Like many mobile devices, the battery in the iPhone is a very difficult to service element. In the majority of cases, owners have to submit their iPhones to Apple or authorized repair centers to switch a worn battery for a new one.
With a large amount of components to remove to access it, as well as adhesives, the battery is quite difficult to replace normally. A user can do so via a self-service repair, but that still requires the rental of specialized tools from Apple itself.
Now, Apple is reportedly preparing to make replacement of the battery a bit easier for consumers. According to five people involved in the manufacturing process speaking to The Information, it may arrive with the iPhone 16 in at least one model.
If successful, it could also be rolled out to all iPhone 17 models.
The proposed change could make things easier, but not by much. After device disassembly, the current process of extracting the battery involves using tweezers to pull on adhesive strips. To add the new battery, a machine and tray is used.
The new version is called electrically-induced adhesive debonding, which involves encasing the battery in metal instead of foil. Using electricity, the battery can be dislodged from the chassis very quickly.
It is still a far cry from smartphones of yesteryear, which allowed users to easily remove the casing to grant them free access to the inside of the device, and the battery. It is thought that Apple will still be constructing the iPhone in a way that it will require specialist tools to take it apart, just like the current models.
Despite being easier, it seems likely that the process will only be accessible to customers well-versed in electronics, and are confident to perform their own repairs.
A regulatory pressure
Apple's work on the technology may have been prompted by regulators attempting to force tech companies into making their hardware more repairable by home users.
In July 2023, the European Council approved regulations to ensure that batteries in many different product categories are replaceable by users. This impacts the iPhone, along with other hardware like electric bike batteries and those used for industrial applications.
While that may be interpreted by some to mean an accessible battery door, but the rule doesn't specify it has to be easy to access. It does say that it can be removed using "commercially available tools," though specialized tools could be used if they are provided free of charge.
In June, Apple announced it was going to expand its Self Service Repair program to a total of 32 European countries, with Canada added in 2025.
Depending on how Apple operates its Self Service Repair program in Europe, this could be enough to meet the requirements of the regulation.
Rumor Score: Possible
Read on AppleInsider
Comments
And yes, Velcro could work amazingly well but is probably too thick unless they use ultra thin velcro.
Going from 'very difficult to replace' to 'a bit easier', definitely won't cut it in the EU if the rule of consumer replacement using everyday tools is applied to iPhones.
Repairability wasn't a consideration when adhesives were introduced. That aspect needs to be tackled with new thinking. It's not difficult.
Throughout its evolution, electronic devices have kept moving towards solid state components. Eventually phones will just be 3 solid blocks of screen, circuitry, and battery, housed inside a waterproof case. Or at the extreme, maybe even just one block containing all three. People who demand user repairability will be frothing at the mouth when that day comes.
In a passive system, heat always goes from the hot side to the cold side. Just continually repeat that in your head. The SoC can hit 200 °F before being down-clocked and decreasing performance until its temperature doesn't go higher than this typical chip limit of somewhere around that temperature. That heat will flow to the colder the parts of device.
By bridging the battery to the SoC attached heat-spreader, the SoC will heat up of the battery faster, even if the heat-spreader is bridged to a cooler glass back or display, and you don't want the battery to be heated. As long as the SoC is the hottest component in the device, its heat will flow to all components in the device that is cooler. The heat-spreader acts as an efficient way to do that and will cause anything directly attached to the heat-spreader to heat up faster.
What Apple does is to use heat-spreaders - graphene-copper tape, some with aluminum substrates - to spread out the heat as much as possible. The batteries are often thermally isolated from the heat-spreaders as much as possible and they are often the last component in the heat transfer process before hitting the outside air.
There are very good reasons to glue batteries to the metal substrates in these devices, but Apple doesn't use these metal substrates as heat-spreaders. They use graphene/copper tape or graphene/copper tape on top of a metal substrate.
As with all engineering, it involves trades. My speculation is that batteries in these devices are typically glued because it increases the reliability of the battery. The adhesive spreads stresses that act on the device across a wide and more evenly distributed area of the battery. This eliminates any point stresses on the battery and thereby increases the batteries' lifetime.
Other solutions to involve making higher expense; thicker & heavier devices, such as a metal brace; a lot of bolts; or can't be made as reliable as glue.
Apple has no problems using screws or bolts. There are many of them in an iPhone, with virtually all components bolted down. The camera modules, the PCB boards, ports, speakers, etc. It's really the batteries and various tapes/shields that are glued. There is a reason for that, and it is likely to increase the reliability of the battery, imo.
For a while, I was thinking that they will design devices with structural batteries, where the metal case or structural metal parts become integral parts of the battery. This minimizes weight, volume, and increases the structural rigidity and robustness of the battery. Like on iPads and MacBooks, the aluminum case is part of the battery and you would have to change out that part of the case to change out of the battery.
This patent, with metal encased batteries where they are bonded to the devices carrier structure, is an interesting in-between?
The Watch batteries were the first usage of metal encased batteries in Apple products. I've thought the reason for that is the Watch gets the most abuse, and therefore drove the need for more reliable batteries first. Haven't taken the step of making the battery and the case one part though.
flexible, performant, cheap - pick 2.