Arizona TSMC facility continues to fight cultural battles, rising costs & logistical hurdl...
Apple chip partner TSMC faces significant barriers that impede the Arizona chip fabrication facility's progress, and the culture clash between American and Taiwanese employees doesn't seem to be getting batter.
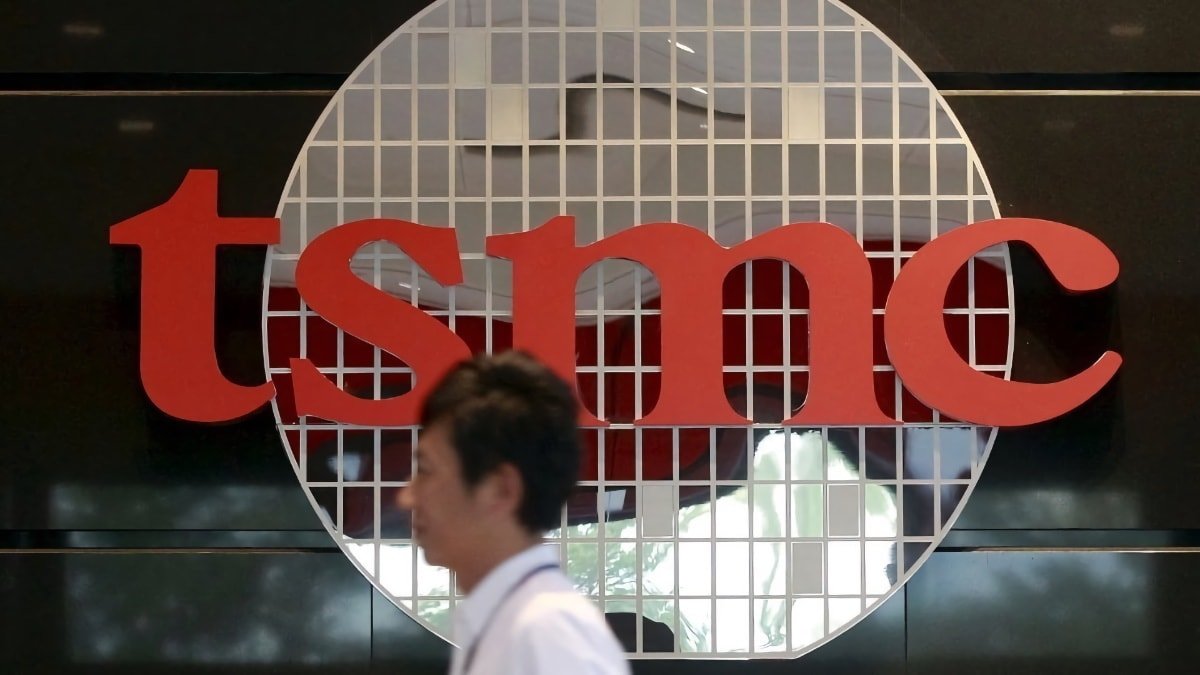
TSMC's Arizona facility grapples with rising costs & logistical hurdles
As the world's leading semiconductor manufacturer, TSMC's decision to expand into the US was met with widespread approval. Its strategic move is intended to secure supply chains and bring critical manufacturing capabilities closer to key markets.
However, the project is now navigating through rising costs and unforeseen logistical issues that could impact timelines and budgets, according to Rest of World.
TSMC's Phoenix facility, a pivotal component of US efforts to revitalize domestic semiconductor production, was initially projected to cost $12 billion. However, the project's expenses are surging due to global supply chain disruptions and inflationary pressures, underscoring its critical role in the industry.
The construction phase of TSMC's Phoenix facility has encountered a myriad of obstacles. These include difficulties in procuring raw materials and managing an international workforce. Notably, American engineers have struggled with the company's rigid hierarchies, while Taiwanese veterans have observed a lack of commitment among their American counterparts, highlighting the complexity of the project.
TSMC insiders said the company's success hinges on a stringent, military-like work culture. Engineers endure 12-hour workdays and often work weekends as well.
The local sourcing of materials has been less than ideal, with many components still needing to be imported from Asia, which adds to costs and logistical complications. Moreover, the project has faced delays in machinery delivery essential for chip manufacturing, which could push back the operational start date.
Effectively addressing the challenges faced by TSMC's Phoenix facility is not only crucial for the company to meet its projected timelines, but also for the US to establish a more resilient semiconductor supply chain. Failing to do so could lead to significant delays and potential disruptions in the industry.
In the meantime, TSMC is preparing a next-generation 1.8nm chip process. The iPhone is expected to adopt 2nm technology by 2026 with the launch of the iPhone 18 series.
Although TSMC's 1.6nm technology is anticipated to debut in the same year, it won't be used in products until 2027.
Read on AppleInsider
Comments
It is not some empty lot or hole in the ground TSMC can walk away from. Culture clash or not, they have to make it work.
If contributing to the product’s probability of success required 12+ hour days for 7 days a week for many weeks, that’s what you did. Having a CEO who believes in doing whatever it takes today to reach the goals, including time and quality goals, is a major influence on a company’s culture, especially when the CEO and corporate leaders are right there too putting in the work in a hands-on capacity that’s appropriate to their roles. But they need to understand and appreciate the value of the technology and product, how it’s made, and what it delivers to customers.
In other words, the culture of the most successful technology companies emphasizes bringing great products to market, not just to make a lot of money. If you deliver great products the money will follow. But delivering great products requires a lot of work. In my opinion, when technology companies were led by technologists and visionaries who totally understood the value of doing the work the right way, they had all of the critical pieces in place for continued success. They also learned how to improve and optimize how they did the work. TSMC is a prime example of how this model works, as were companies like Intel, Motorola, GE, Boeing, and Apple in their early days.
That was then, and now is now. Today the culture of most companies emphasizes bringing great financial value to investors and shareholders, whatever it takes. Goodbye to the engineers in CEO roles. Hello to the money men/women running the company. Sure, the product still has to be great, but doing the work is nowan overhead process and cost that can be farmed out to the lowest qualified bidder. No deep domain expertise needs to be grown inside the company, just go out buy it. Of course the degree and extent to how this money driven culture is embedded varies from company to company. Apple seems to maintain enough focus on the engineering aspects of what they do to ensure that those who are doing the work have Apple engineers working alongside them. Apple has certainly outsourced a ton of their product manufacturing capabilities, but at the same time they’ve pulled in significant critical pieces like Apple Silicon so as not to be dependent on another supplier they cannot totally control.
Does Apple have a predominant product driven culture or profit driven culture? I think it’s still up in the air. One could argue that the change in command from Steve Jobs to Tim Cook marked a transition point from one to the other. But I also believe that Steve Jobs picked Tim Cook because he knew Tim would not totally succumb to the profit mongers and would keep the product culture alive and well, at least to the extent that is possible given the current nature of how products are dependent on global influences. The TSMC struggles in Phoenix don’t elicit a lot of confidence in the US’s ability to reset its cultural focus from profits and financial success back to one of producing great products that we’re proud of. We’ve moved on to a “Show me the money” culture in the workplace while TSMC is still focused on doing the work to reach goals, no matter the personal sacrifices required. Maybe we’ll eventually land on something in the middle, but my hopes are not high.
Intel plans on catching up and passing TSMC. We all know what happens to plans, so probably not. But, Intel as a second source manufacturer of Apple Silicon isn't a bad idea either, or Samsung Semi. It would require Apple to sell more products, so long road to go on that.
There's a reason manufacturing of semiconductors and other goods have moved to Asia. There are way more engineers available in Asia; these are needed in large numbers to run a modern factory. Engineers in Asia work longer hours without complaint, so no surprise TSMC is finding American engineers difficult to work with.
Many stories, the books and movies that could be made...I still have many boxes of my Dad's efforts that contributed to the start-up and the take-off of FedEx.
As @dewme mentioned "If contributing to the product’s probability of success required 12+ hour days for 7 days a week for many weeks, that’s what you did."
In the case of FedEx, it was years of the efforts he mentions.
When my Dad retired, he was flying the DC-10 on the international routes. Chief Pilot/VP of Flight Operations, and held the Pilot Seniority position of #1.
Do you agree? What sort of compromises will have to be made? TSMC’s corporate culture will have to deal with US labor laws, among other obstacles.
ps. The Japanese managers were mostly limited to three year stents inside the United States so they wouldn’t become too Americanized. They built a Japanese school for their kids to go to.
The reason a "modern factory" requires a large number of "engineers" is that in China, production technology assumes a large number of poor, desperate people willing to be worked to death. As the Chinese population shrinks to 500 million by the year 2100, the production technology will change to rely more heavily on actual robots, not humans treated like robots. In other words, China will become more like the US and Europe.
The result will not be a huge increase in prices, but rather a lowering of corporate profits.